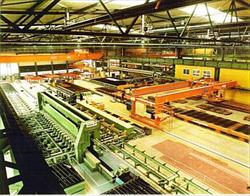
Modern Gemi İmalatı![]()
1. 21. Yüzyılda Gemi İnşaat Sektörü Dünya gemi inşaa pazarı tersane sahiplerinin ve armatörlerin ayrı ayrı baskın olduğu dönemler arasında büyük dalgalanmalar yaşamıştır. Tersanelerde artık kapasite olduğu zamanlarda rekabet çetindir. Artık tersane kapasitesinin fazları genellikle yetersiz tersane kapasitesinin fazlarından daha uzundur. Artık kapasite zamanlarında, sadece daha kârlı biçimde çalışan rekabetçi tersaneler ayakta kalabilmektedir. Dünyada durum 2009 yılında şu şekildedir: § Azalan talepten ötürü tersane kapasitesinde fazlalık oluşmuştur § Asya’da, geçtiğimiz on yılda gemi inşaa kapasitesi artmıştır. Japonya, devre dışı kalmış tersane kapasitesine tekrar işlerlik kazandırmıştır. Çin ve Kore yeni tersaneler yaparak ve mevcut tersaneleri büyüterek kapasite artışı sağlamıştır § Sadece savaş gemisi üreten Amerikan ve eski Sovyetler Birliği ülkelerindeki tersanelerde sivil pazara giriş yapma teşebbüsleriyle artık kapasiteyi fazlalaştırmıştır § Batı Avrupa tersaneleri sübvansiyonlar karşılığında kapasite limitleri konusunda politik uygulamaların yürütüldüğü tek dünya bölgesidir. Küresel bir mücadele alanı yoktu... Sübvansiyonlar ve kur oranı gibi farklı etmenler doğrultusunda Asya tersaneleri son yıllarda öne çıkmıştır. Pazarın genel karakteri, kolay giriş ve zor çıkış şeklinde olduğundan çetin bir rekabet ve azalan kârlar vardır. Alıcıların hakim olduğu zamanlarda tersaneler, yüksek kalitedeki gemileri en kısa zamanda ve en ucuz maliyetle sunmak zorundadır. Daha az rekabet gücü olan tersaneler, yeniden kârlı hale gelmek için süreçlerini iyileştirmek zorundadır. İşçiliğin pahalı olduğu ülkelerdeki tersaneler bu sorunlara karşı üretim yöntemlerinin modernizasyonu ve otomasyonu ile karşılık vermiştir. Genellikle tüm süreç, projelendirme, detaylı tasarım, satınalma, planlama ve üretim ile birlikte düşünülür. Böyle bir dönüşümün en tipik örneği, Baltık kıyısındaki (Flensburg, Kiel, Wismar, Stralsund ve Wolgast gibi) şehirlerde bulunan klasik tersanelerin, modern yüksek performanslı tersanelere dönüştüğü Alman tersaneleridir. Her alanda hedef, fiyat, teslim süresi ve kalite konularında rekabetçiliği geliştirmektir. Yüksek rekabetçi teknoloji için aşağıdaki süreçlerin detaylı olarak geliştirilmesi gerekir: · Taşeron kullanmak (Montaj tersanesi kavramı) · Derli Toplu Üretim (Tersane alanının küçülmesi) · Kapalı alanda üretim tesisi (hava koşullarından bağımsız olarak sabit kalite) (Ekler Şekil 2) · İnsan ve malzemeye yakınlık · Ürün portföyünde esnekliği korurken üretim ve iletim otomasyonu (Ekler Şekil 3) · Levha, profil, panel ve mikro ağlar için montaj hattında üretim · Kaynak ve kesmede yüksek performanslı teknolojiler · Ayar ve düzeltme işinin azalması için hassas üretim (malzeme ve üretim teknolojisiyle ilgili) · Planlama ve kontrol Cad, CAP, CAM ve CNC üretimle otomasyon · Farklı üretim alanları arası ortak BT ve lojistik platformları 2. Üretim Teknolojisi ve Lojistik 2.1 Giriş
Ürünün karmaşık yapısından ötürü (ortalama bir gemi için 20000’den fazla parça, gitgide karmaşıklaşan ara-montajlarla sıralı üretim adımları) gemi inşaatı karmaşık planlama ve üretim süreçleri içerir. Üretim teknolojisini ve tersane yerleşimini büyük oranda ürün yapısı ile malzeme akışı belirler. Parça ve ara gruplarda montaj hattının yaygınlaşması ile montaj ve iletim otomasyonu önem kazanmıştır. Kesme, markalama, tornalama, bükme ve kaynaklı imalatlar için CNC makineleri tüm modern tersanelerde bir standarttır. Bu makineler, tersanelere özel planlama ve kontrol sistemi vasıtasıyla CAD sistemlerinden gerekli veriyi anında alırlar. Sistem ayrıca üretim istasyonları arasındaki malzeme akışını planlar ve izler. Yüksek otomasyonlu bu kurulum şunlara imkan sağlar: · Ürün ve siparişlere yönelik parça akışının şeffaflaşması · Parça ve siparişlerin kısmi kontrolü · Üretim sürecinde yaşanan sıkıntılara hızlı müdahale · Üretim kapasitesinin etkin kullanımı · Stoklarda ve işlem sürelerinde tasarruf Şekil 1, Modern tersanelerde 2008 yılında otomasyonun derecesini gösterir. Şekil 1: Gemi üretiminde otomasyon dereceleri; Parça imalatı; Panel imalatı; Hacim montajı; Güverte ve kızak montajı Otomasyon derecesi ürün portföyü, üretim teknolojisi ve tersane boyutuna bağlıdır. Genellikle otomasyon derecesi, parça imalatından güverte montajına doğru azalır. Bunun sebebi karmaşıklığın artması, ara montaj gruplarının azalması ve otomasyonun teknik ve/veya ekonomik olarak yapılabilir olmamasıdır. İlerleyen sayfalarda kaynak teknolojisi daha detaylı tartışılacaktır. Kaynak aktivitelerinin tersane üretkenliğine büyük etkisi vardır. Gemi imalatı adam saatlerinin yüzde 40’lık kısmı kaynaklı imalattan gelir. Bir gemi gövdesindeki kaynak uzunluğu gemi tipine, boyutuna, levha boyutuna ve bölüm sonlarına bağlı olarak değişir. Kaynakların yüzde 80’lik kısmı bindirme, yüzde 20’lik kısmı ise alın kaynağıdır. Kaynak malzemesinin ağırlığı toplam gövde ağırlığının yüzde 3-5’lik kısmını oluşturur. Kaynakların ortalama yüzde 70 kadarı en azından kısmen otomatiktir. Kaynak kalitesi, diğer etkenler kadar kaynağa hazırlık aşamasındaki hassasiyete de bağlıdır (levhaları ve profillerin kesilmesi) 2.2 Levha ve Profil Kesimi Temelde tersanede bulunan tüm çelik malzeme bir levha veya profil kesim işlemi görür. Bundan dolayı bu alanda otomasyona yönelik çok fırsat vardır. Levha kesiminde, CNC kesim makineleri ve frezeler otomatik vinçler ile öne arkaya hareket ettirilirler. Dahili bir kontrol istasyonu başlangıç ve hedef konumlarını vince gönderir. Kontrol ünitesi ayrıca makinelerin CNC programlarını koordine eder ve talebin tamamlandığını da kontrol eder. Kontrol istasyonu tersanenin planlama ve kontrol merkezine bağlıdır. Depolama alanlarında markalama özelliğine sahip bilgisayar destekli vinçler kullanılır. CNC kesim makineleri oksi-asetilen, sulu plazma ve kuru plazma kesicilerle donatılmıştır. Makineler tek veya çift tabla üzerinde 4 x16 metre plakalar kesebilir. A sınıfından E32 sınıfına tüm çelikler kesilir. Levhalar kaplanır(çinko kaplama 20μm kalınlıkta) Sac kalınlığı 5 ila Robot teknolojisi gemi üretimine profil kesim sayesinde girmiştir. 6 eksenli, mafsallı, gezer vinçlii robotlar klasik kesme makinelerinin ve elle kesimin yerini almıştır. Modern profil kesimi otomatizedir. Teknolojinin özünde, robotik bir kesici, kesme tablası ve kaynak duman egzozuyla beraber bir kesme hücresi vardır. Profiller, kesme makinesine verilmeden önce bilgisayar destekli depolardan tek tek alınır, döner konveyörlerle ve gidip gelen iletim mekanizmalarıyla gönderilirler, ölçüm cihazıyla hassas olarak kesim ölçüsü markalanır. Plazma kesimi halen daha en popüler kesim teknolojisidir. CNC Plazma kesim tek defada 2.3 Düz Panel Üretimi Düz paneller uzunlamasına ve enlemesine uzanan payandalara sahip alın kaynaklı levhalardan oluşur. Payandalar levhalara bindirme kaynakla eklenmiştir. Tipik panel ölçüleri Böyle bir hattın standart ekipmanları aşağıdaki gibidir: · Kısmen otomatik tek taraflı kaynak hattı · CNC kesme, pürüzlendirme ve markalama vinci · Profilleri yerleştirme ve sabitleme vinci · Kısmen otomatik bindirme kaynak sehpası · Tümleşik mekanik iletim teknolojisiyle birlikte yer ekipmanları ve montaj ve ekipman destek vinci Düz montajlarda (örneğin Hem tek hem de çift taraflı kaynak alın kaynağı için kullanılmıştır. Tek taraflı kaynak, zaman kaybına yol açan döndürme ve gerekli altyapıdan tasarruf sağlar; ancak ekipman standartları daha karmaşıktır, daha fazla teknolojik disiplin gerekir ve aynı kaynak kalitesi daha fazla ön hazırlık gerektirir. Günümüzde tek taraflı kaynak uygulamalarında 22 metreye kadar uzunluklarda, 5 ila Tek taraflı kaynak sitasyonları bir destek tablasıyla beraber gelir. Bakır altlık ve fikstür ile hassas yerleştirme ve kaynak noktasını sabitlemek için gerekli kelepçeler en önemli elemanlardır. Yaygın kullanılan teknolojiler mekanik, manyetik ve vakum sistemleridir. Her bir alternatif 7 ton/metre gerilme kuvvetine dayanır. Manyetik sistemler en ucuz sistemlerdir. Ancak sadece mıknatıslanma özelliği olan parçalarda kullanılırlar. Maksimum gerilme gücü malzeme kalınlığına bağlıdır. Destek tablasının bir yarısının yüksekliği ayarlanabilir; böylece farklı kalınlıklarda malzemeler kaynaklanabilir. Seçilen tozaltı teknolojisi performans ve kalite gereksinimleri kadar kaynak hazırlığı imkanına göre de belirlenir. Tek taraflı kaynak için, tozaltı mikro enjeksiyon(SAW-FMI) ve tozaltı seri ark yöntemleri popülerdir. Bu yöntemler bir kaynak için iki veya üç tel kullanırlarken masif ve özlü elektrod vardır. Yüksek kaynak hızlarında kaliteli uygulama SAW-FMI yöntemi tercih edilebilir.Mikro enjeksiyon tel yönteminde, Ti-B(Titanyum-Bor) alaşımı kaynak elektrodu bir veya iki masif elektrodla birlikte enjekte edilir. Geliştirilmiş(elektrodların ergime anında aralarındaki enerji dengesi geliştirilmiştir) seri ark yöntemi, tek taraflı kaynak daha büyük boşluk toleranslarıyla yapılabilir (±1.0mm) Tek taraflı kaynak istasyonundan sonra bir kesme-taşlama-markalama tezgahı vardır. CNC makinesi CAD ofisine bağlıdır. Çok görevli tezgah formları keser ve köşeleri hazırlar; hava veya sürtünme yardımıyla kaplanır, plazma veya mürekkep ile levhayı profillerin düzgün yerleştirilmesi ve bindirme kaynağı için markalar. Genellikle makinenin üzerinde kesim için üç kafalı bir oksi-asetilen kesme şaluması vardır. Taşlama ve markalama aletleri 12 metre/dakika hızlara kadar çalışabilirler. Profil yerleştirme ve sabitleme tezgahı profilleri paletten almak ve levha üzerinde hassas biçimde markalanmış hatlara yerleştirmek üzere özel bir manyetik teknik kullanır. Daha sonrasında otomatik bir sabitleme işlemi ile levha ve profil arasındaki hava alınır. Sabitleme, levhanın her iki tarafında belirlenmiş bir rotaya uygun yapılır. Paletler bir palet taşıyıcı üzerinde bulunur. Böylece tezgah kısa sürede işlemi gerçekleştirebilir. Makine, Hareketli bindirme kaynak tezgahları, levha ve profillere bir panel hattı boyunca sadece enine kaynakları atabilir. Gerekli kapasiteye bağlı olarak, tandem olarak çalışacak kaynak kafaları ile çift bindirme kaynakları yapılabilir. Kolay otomasyondan ötürü, özellikle çoklu kaynak kafalarına sahip yüksek performans uygulamalarında MIG ve MAG kaynakları yaygın olarak bulunur. Tek veya çift taşıyıcılı tezgahlar vardır. Bu tezgahların bazılarında tek taşıyıcı bazılarında çift taşıyıcı vardır; bu taşıyıcıların bazıları tandem kaynak kafasıyla (tipik Alman tersaneleri) ve her birinde birer taşıyıcı olan çift tezgahta 6 taneye kadar tandem kaynak kafasıyla donatılmıştır (tipik Kore ve Japon tersaneleri). Kaynak makineleri tek kişiyle çalışabilecek ölçüde otomatiktir. Operatörün kabaca yerleştirmesinden sonra kaynak kafası sensör vasıtasıyla kaynak işlemini sürdürür. Sürekli veya kesikli kaynaklar mümkündür. Kaynak parametreleri bindirme kaynak kalınlığa bağlı belirlenir, programlanır ve depolanır. Kaynak gazları ve parlama konusunda sağlık yönetmelikleri takip edilir. Tek tel ve modern tandem MIG/MAG kaynakları arasındaki inanılmaz performans farkı açıkça görülmektedir. MIG/MAG tandem kaynağı iki şekilde karşımıza çıkar: · 2 ayrı elektrod aynı kaynak kafası içinde birbirine yakın yerleştirilir ( · 2 elektrod iki ayrı kaynak kafasına yerleştirilmiştir (mesafe 80 mm’ye kadar çıkabilir) ve iki ayrı kaynak havuzunda ergirler (dikiş genişliği 3,5 ilâ Tandem kaynakta, her bir elektrodun kendine ait elektrik beslemesi, tel beslemesi ve kontrolü vardır. Böylece her elektrodun kendine has akım yoğunluğu ve ark voltaj değerleri olur. Genelde ilk elektrodun akım yoğunluğu daha derin kaynak penetrasyonu elde edebilmek için daha yüksek olur. İkinci elektrod daha fazla voltajla kaynak dikişinin arzu edilen genişliğe ulaşmasına yardımcı olur. 10 mm’den küçük elektrod mesafelerinde, darbe süperpozisyonu kullanılarak arklar arasında etkileşim olması engellenmektedir. Daha büyük elektrod mesafeleri için bu geçerli değildir. MIG/MAG tandem kaynağında, yüksek ergme gücü yüksek kaynak hızını beraber getirirken birim kaynak uzunluğu başına harcanan enerji tek tel sistemden farklı olmamaktır. Tandem kaynakta yüksek kaynak hızı daha uzun bir kaynak havuzu sayesinde elde edilmektedir. Ayrıca ön ısınma ve son ısınma bölgeleri daha uzundur. Bu özellik yeterli kaynak penetrasyonu ve kaynak havuzunun gazlardan arınması açısından yardımcı olmaktadır. Bu durum, alüminyum kaynağı ve gemi sektöründe sık rastlanan astar boya ile kaplanmış sacların kaynağı için olumlu bir noktadır. Bindirme kaynaktan sonra, kiriş ve dikmeler dik biçimde ana payanda yönünde kaynaklanır. Bu operasyon, yarı otomatik MIG/MAG kaynak cihazları, elle kaynak sistemleri ve taşıma araçları ile donatılmış bir istasyonda yapılır. Ekipman, işçilere uzaktan kumandalı ceraskallarla iletilir. Özel asansörler işçiler, daha yüksekteki noktalara ulaşarak merdiven ve iskelenin kurulumunu yaparlar. Levha ve kirişler arasında, kiriş ve dikmeler arasında ve kiriş ve profil arasında kalan diğer bindirme kaynaklar da MIG/MAG kaynak yöntemiyle ve yordamıyla yapılır. Ekipman tezgahı kaynak işlemini ve egzost gazlarını uzaklaştırmak için gerekli ekipmanı desteklemek için kullanılan bir platformdur ve kaynakçıya uzaktan kumandalı ceraskallarla ulaştırılır. Bu teknolojimim yerini 2.4 Mikro panel Üretimi Mikro paneller, en fazla Yapıya bağlı olarak, ark kaynağı işlerinin yüzde 60’a kadar olan kısmı robotlar tarafından yapılabilir. Karışık gazlı, masif veya örtülü elektrodlu tek tel MIG/MAG teknolojisi kullanılır. Kaynak hızı dolgu malzemesine ve iş parçasının yüzey durumuna bağlıdır.
3. Sonuç Gemi inşaat sektörü düşük teknoloji kullanılan bir endüstri görünümümünden sıyrılarak yüksek teknolojili bir endüstri olma yolunda hızla ilerlemektedir. Ara-montaj parça üretimleri halihazırda otomasyon yardımıyla yapılmaktadır. CNC kesme, bükme ve kenarların düzeltilmesi ve robot kaynak cihazları gemi inşaasının yeni yüzünü temsil eder. Bilgisayar destekli planlama ve simülasyon sistemleri tersanedeki tüm süreçlerin şeffaflaşmasını sağlar. Bu alandaki ilerleme devam edecektir. Kavisli gemi yapıları için kaynak robotları daha fazla kullanılacaktır. Yeni sensörler kaynak ortamını daha iyi ortaya koyacak (kaynak tipi, hattı, geçiş kısmı, hava boşluğu) ve dışsal kaynak kontrolü için altyapı oluşturacaktır. Robotların bilgisayar ortamında programlanması robotların zeka ve hissetme becerilerinin yardımıyla daha da basitleştirilecektir. Lazer teknolojisi de kesme ve kaynak teknolojisine bir ivme kazandıracaktır. Günümüzde lazerler ince plakalarda (s< İlginizi çekebilir... Gemilerde Tankerlerde Gaz Serbest Bırakma (Gas Free) İşlemiSezer ASLAN
Yangın, Acil Durumlar Deprem Eğitim Uzmanı
Yangın Risk Analizi, Danışman, NFPA Member... Koruma Fonksiyonlu Bir Yangın Pompasının Optimal Bir TasarımıYangından korunma, ulusal ekonomik ve sosyal kalkınmanın önemli bir parçasıdır, sosyalist piyasa ekonomisinin gelişmesinin vazgeçilmez bir garantisidi... Gemilerde Yangın Söndürme SistemleriÖmer AYDIN / Control Technic Elektrik Ltd.... |
||||
©2025 B2B Medya - Teknik Sektör Yayıncılığı A.Ş. | Sektörel Yayıncılar Derneği üyesidir. | Çerez Bilgisi ve Gizlilik Politikamız için lütfen tıklayınız.